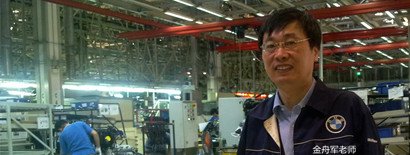
上海咨詢公司精益?生產管理培訓公開課咨詢?課程—歡迎企業培訓公開課和機構合作垂詢
金舟軍老師 手機/微信:13816949004 QQ郵箱:923503608@qq.com
以應用為導向的精益生產培訓,學員培訓后就會應用精益生產管理,金舟軍老師通過嚴格的培訓流程確保顧客滿意
請點擊查看—金舟軍質量管理工具培訓咨詢實施流程
精益生產?培訓講師質量專家金舟軍,精益生產培訓咨詢機構上海科租企業管理咨詢有限公司,是專業、實戰的培訓,精益生產培訓,培訓班和企業內訓請垂詢培訓大綱,精益生產培訓資料光盤贈送
最有價值?的精益生產管理?培訓公司
上海科租企業管理咨詢有限公司金舟軍老師自辦精益生產?培訓咨詢公司,培訓老師自辦咨詢公司省出了業務費用和老板利潤,客戶的培訓費全部變為培訓老師的培訓費,能為客戶提供優質服務,客戶培訓價值最大化值 。只要學員參加過質量培訓課程,將為學員提供終生的培訓課程答疑。
最具專業的精益生產?培訓講師
金舟軍二十多年專業從事精益生產?培訓講師,專業涉及質量管理和精益生產課程,客戶涉及世界五百強企業, 每個培訓項目的客戶都有培訓現場的視頻和照片為證。金舟軍老師課程以應用為導向,課堂上只講干貨,絕不以無關的游戲打發時間。
培訓客戶-全部有客戶培訓現場照片、視頻為證!

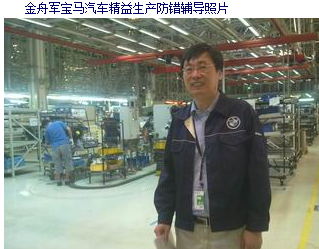
精益生?產管理培訓

重慶長安汽車、上海延鋒韋世通、上海NEC、上海德爾福、武漢東風汽車、江蘇東風起亞、江蘇麥格納、安徽康佳電器、、安徽博西華、上海奧托立夫、浙江海信惠爾浦、沈陽寶馬汽車、上海大金空調、遼寧大連固特異輪胎、長春大眾集團、湖北武漢佛吉亞、上汽集團、吉林一汽集團、廣西上汽通用五菱、廣西玉林重工、江西長力股份 北京北汽福田、深圳中興通迅、福建新能源科技、湖南三一重工、蘇州恩斯克軸承、河北天威光伏、武漢哈金森、蘇州力特奧維斯、重慶 嘉陵集團 福建奔馳汽車、遼寧大連大眾變速箱 廣東廣州京信通信、深圳中興通訊 河南利達光電 河南新鄉豫新 河北萊尼、山東萊尼 、山東勝地、陜西中航、湖南時代電氣、天津中核
精益?生產管理培訓課程公開課視?頻--點擊圖片即觀看好看視?頻或優酷視?頻相應培訓視頻
精益?生產管理培訓課程公開課視?頻--點擊圖片即觀看好看視?頻或優酷視?頻相應培訓視頻
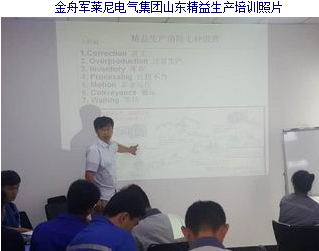
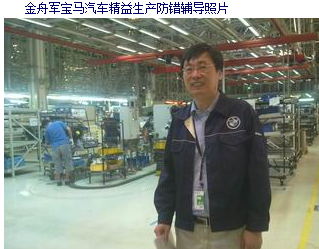
精益生?產管理培訓
課程公開課大綱
一.培訓目的:通過學習,學員能掌握精益生產的方法,并能利用拉動式準時化生產、目視管理、看板管理、
價值流分析、流線生產線布置等方法消除企業中的七種浪費。
二.培訓對象:生產管理、質量管理、現場管理人員和班組長。
三.課程內容
1.精益生產產生背景 金舟軍原創抄襲必告
生產的本質
兩種生產方式
TPS豐田生產方式
福特大規模少品種生產方式
案例討論-兩種生產方式各自的金優缺點
2.精益生產原理
精益生產系統
實施精益生產的基礎
案例討論-實施精益生產的基礎有哪些
3.精益思想的五個基本原則
價值原則VALUE
價值流原則VALUESTREAM
流動原則FLOW
拉動原則PULL
盡善盡美原則PERFECTION
案例討論-盡善盡美原則包括哪些內容
4.精益生產消除七種浪費
浪費的定義MUDA
過量生產浪費
庫存浪費
搬運浪費
返工浪費
過程不當浪費
多余動作浪費
等待浪費
案例討論-過量生產浪費產生的原因有哪些
5.柔性生產
通過時間
進料倉庫到出貨倉庫時間(DTD)
制造周期時間(MCT)
案例討論-怎樣減小制造舟周期時間
6.價值流分析 金舟軍原創抄襲必告
精益生產創造價值的原則
生產增值比率
過程價值流分析方法
創造價值的過程
公開的浪費的過程
隱蔽的浪費的過程
價值流程圖ValueStreamMapping
案例討論-客戶某一生產過程價值流分析
7.過程風險分析
過程風險嚴重度
過程風險發生率
過程風險評價
過程風險的預防措施
案例討論-客戶某一生產過程風險的舟預防措施
8.作業切換時間
內部切換時間
外部切換時間
快速換模SMED
作業切換時間減小的方法
案例討論-客戶某一生產過程外部切換時間減少
9.單件流 金舟軍原創抄襲必告
無停頓和堵塞的生產流程
機器別布置
工藝順布置CELL
單元U型平面布局圖
案例討論-客戶某一生產過程U型平面布局圖
10.節拍生產
用戶節拍是工廠的脈搏
循環時間Cycletime與節拍時間Takttime
基于節拍時間優化循環時間
案例討論-怎樣實現某產品生產各工序循環時間與節拍時間一致
11.拉動生產
只有當用戶訂貨時才生產
精益生產過程自動調整
推動與拉動
生產信息和物料的流動
看板Kanban管理
看板運行流程
看板主要內容
看板數量計算
案例討論-客戶某一生產過程看板數量計算
12.零缺陷 金舟軍原創抄襲必告
過程質量決定產品質量
兩種零缺陷及其實現方法
停產分析解決問題
5Why找出根本因
首次通過率
案例討論-客戶某一生產過程實現零缺陷的方法
13.自働化
防錯=自働化
自働化兩大功能
三種檢驗方法
判斷檢驗
信息檢驗
溯源檢驗
案例討論-客戶某一生產過程溯源檢驗實現零缺陷的方法
14.防錯
十種人為錯誤
人員三個方面的錯誤
防錯兩種功能
三種類型防錯方法
觸碰式防錯法
固定數值防錯法
動作步驟探測防錯法
案例討論-客戶某一生產過程溯源檢驗實現零缺陷的方法
15.TPM全面設備維護
設備管理七大損失
OEE設備綜合效率
時間開動率
性能開動率 金舟軍原創抄襲必告
合格品率
自主維護AutonomousMaintenance
自主維護三個活動
自主點檢檢查表項目
日常點檢表范例
設備清掃清單
預測性維護
預防性維護
計劃維護
案例討論-設計一個自主點檢軍檢查表
16.透明工廠
可以認清與額定值的偏差
目視管理
顏色管理
生產目視化管理
目視化每日/周/月維護
目視化質量狀況
目視化產品檢驗狀態
定置管理圖
案例討論-螺絲擰緊顏色管理
17.持續改進CIP
持續改進Kaizen
系統改進步驟
糾正措施vs糾正
確定根本原因三步法
—直到達到卓越的過程。
案例討論-三步法分析根本原因
18.標準化作業
標準作業指導書
標準作業的生產節拍
標準作業步驟或要素
標準在制品量 金舟軍原創抄襲必告
每項改進的基礎
案例討論-三步法分析根本原因
19.現場負責
出現在距創造價值近的地方
經理現場負責
工廠指標在現場
員工參與編制作業指導書
案例討論-為什么要員工參與編制作業指導書
20.零浪費
減少浪費是持久的挑戰.
識別浪費的方法
減少浪費的方法
案例討論-實現零浪費的措施有哪些.
21.5S實施精益生產的基礎
整理整頓清掃清潔素養
必需品和非必需品的基準表
清掃清單
案例討論-5個S之間是什么關系
22.定置管理
工藝研究確定物流布置
人機工程確定工位布置
案例討論-工位布置置要考慮哪些因素
四.課程學時:每天7小時共2-8天
精益生產培訓
寶馬汽車VPS課程大綱
本課程為精益生產的實戰課程,培訓師金舟軍作為寶馬汽車精益生產VPS講師參與開發中國寶馬中國精益
生產VPS培訓課程,并為中國寶馬開展過十幾天的各階層精益生產VPS培訓,本培訓教材即是寶馬中文精益生產VPS
教材。具有實戰簡潔之特點,使學員掌握五百強企業精益生產之精華。
一.培訓目的:通過學習,學員能掌握精益生產的方法,并能利用過拉動式準時化生產、目視管理、看板管理、價
值流分析、流線生產線布置方法消除七種浪費。。
二.培訓對象:產品設計開發人員、售前售后工程師、過程設計核心成員。
三.課程內容
精益生產產生背景
精益思想的五個基本原則
實施精益生產的基礎
精益生產消除七種浪費
精益生產創造價值的原則
創造價值的定向原則
常見的七大浪費
過量生產浪費
庫存浪費
搬運浪費
返工浪費
過程不當浪費
多余動作浪費
等待浪費
價值流分析
10項精益生產過程原則
靈活性
-精益生產的核心強勢
單件流
-無停頓和堵塞的生產流程
節拍
—用戶節拍是工廠的脈搏
拉動
-只有當用戶訂貨時才生產
零缺陷
—過程質量決定產品質量
透明工廠
—可以認清與額定值的偏差
持續改進CIP
—直到達到卓越的過程。
標準化作業
-每項改進的基礎。
現場負責
-出現在距創造價值近的地方
零浪費
-減少浪費是持久的挑戰.
5S實施精益生產的基礎
四.課程學時:每天七小時共2天
精益生產培訓機構上海科租企業管理咨詢有限公司
精益生產及其產生
精益生產,又稱精良生產,其中“精”表示精良、精確、精美;“益”表示利益、效益等等。精益生產就是及時制造,消滅故障,消除一切浪費,向零缺陷、零庫存進軍。它是美國麻省理工學院在一項名為“國際汽車計劃”的研究項目中提出來的。它們在做了大量的調查和對比后,認為日本豐田汽車公司的生產方式是最適用于現代制造企業的一種生產組織管理方式,稱之為精益生產,以針對美國大量生產方式過干臃腫的弊病。精益生產綜合了大量生產與單件生產方式的優點,力求在大量生產中實現多品種和高質量產品的低成本生產。
一、精益生產的產生與推廣
20世紀初,從美國福特汽車公司創立第一條汽車生產流水線以來,大規模的生產流水線一直是現代工業生產的主要特征。大規模生產方式是以標準化、大批量生產來降低生產成本,提高生產效率的。這種方式適應了美國當時的國情,汽車生產流水線的產生,一舉把汽車從少數富翁的奢侈品變成了大眾化的交通工具,美國汽車工業也由此迅速成長為美國的一大支往產業,并帶動和促進了包括鋼鐵、玻璃、橡膠、機電以至交通服務業等在內的一大批產業的發展。大規模流水生產在生產技術以及生產管理史上具有極為重要的意義。但是第二次世界大依以后,社會進入了一個市場需求向多樣化發展的新階
段,相應地要求工業生產向多品種、小批量的方向發展,單品種、大批量的流水生產方式的弱點就日漸明顯了。為了順應這樣的時代要求,由日本豐田汽車公司首創的精益生產,作為多品種、小批量混合生產條件下的高質量、低消耗進行生產的方式在實踐中摸索、創造出來了。
1950年,日本的豐田英二考察了美國底持律的福特公司的轎車廠。當時這個廠每天能生產7000輛轎車,比日本豐田公司一年的產量還要多。但豐田在他的考察報告中卻寫道:“那里的生產體制還有改進的可能”。
戰后的日本經濟蕭條,缺少資金和外匯。怎樣建立日本的汽車工業?照搬美國的大量生產方式,還是按照日本的國情,另謀出路,豐田選擇了后者。日本的社會文化背景與美國是大不相同的,日本的家族觀念、服從紀律和團隊精神是美國人所沒有的,日本沒有美國那么多的外籍工人,也沒有美國的生活方式所形成的自由散漫和個人主義的泛濫。日本的經濟和技術基礎也與美國相距甚遠。日本當時沒有可能全面引進美國成套設備來生產汽車,而且日本當時所期望的生產量僅為美國的幾十分之一。“規模經濟”法則在這里面臨著考驗。改進改進對于每個人都是理所當然,每個人都要愉快地為改進出一份力,改進是我們日常工作的出發點。小改進將立即實施。每個過程都能夠作改進并且每項改進都注入某個標準中。每個標準又是繼續改進的出發點。
Kaizen
Kaizen意味著改進,涉及每一個人、每一環節的連續不斷的改進:從最高的管理部門、管理人員到工人。持續改善的策略是是日本人競爭成功的關鍵
糾正措施vs糾正
為一勞永逸永久地解決問題,使問題不再發生,要針對問題的根本原因采取糾正措施,而非僅針對問題本身采取
糾正。
糾正措施correctiveaction
為消除已發現的不合格或其他不期望情況的原因所采取的措施
糾正correction
為消除已發現的不合格所采取的措施。
標準
標準通常是最聰明的解決辦法。使經驗交流變得容易一些,每個過程都遵循某個標準。我們的創造力將不斷地提高這些標準。
標準作業指導書
標準作業是指把生產過程中的各種要素(人、機、料、法、環、測)進行最佳組合,按生產要求制定出相適應的作業標準。作業人員按照作業標準進行操作。
現場負責
經理在現場辦公,定期與工人對話,直接就在發生問題的地方解決問題。
三現主義指的是現場、現物、現實,當發生問題的時候,管理者要快速去“現場”,觀察“現物”,探究“現實”,找出問題原因和落實解決辦法。