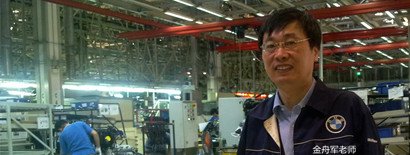
上海咨詢公司六??西格瑪管理綠帶黑?帶培訓咨詢課程—歡迎企業培訓公開課和機構合作垂詢
金舟軍老師 手機/微信:13816949004 QQ郵箱:923503608@qq.com
專業、實戰、以應用為導向的六西格瑪&設計六西格瑪DFSS綠帶黑帶培訓公開課,學員培訓后就會應用六西格瑪&DFSS,金舟軍老師通過嚴格的培訓流程確保顧客滿意
請點擊查看—金舟軍質量管理工具培訓咨詢實施流程
六西格瑪培訓講師質量專家金舟軍,六西格瑪管理培訓咨詢機構上海科租企業管理咨詢有限公司,是專業、實戰的培訓,培訓班和企業內訓請垂詢,六西格瑪培訓資料光盤贈送,歡迎培訓機構合作
最有價值的六西格瑪培訓公司
上海科租企業管理咨詢有限公司金舟軍老師自辦六西格瑪培訓咨詢公司,培訓老師自辦公司省出了業務費用和老板利潤,客戶的培訓費全部變為培訓老師的培訓費,能為客戶提供優質服務,客戶培訓價值最大化值 。只要學員參加過質量培訓課程,將為學員提供終生的培訓課程答疑。
最具專業的六西格瑪管理培訓講師
金舟軍二十多年專業從事六西格瑪管理培訓講師,專業涉及質量管理和精益生產課程,客戶涉及世界五百強企業, 每個培訓項目的客戶都有培訓現場的視頻和照片為證。金舟軍老師課程以應用為導向,課堂上只講干貨,絕不以無關的游戲打發時間。
培訓的客戶-全部有客戶培訓現場照片、視頻為證!


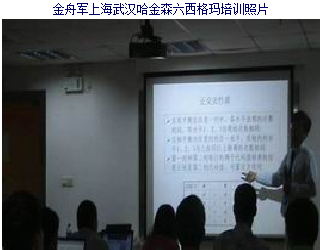
六西格瑪培訓
一.培訓對象6SIGMA項目、TS和ISO質量體系的質量及技術人員

重慶長安汽車、上海延鋒韋世通、上海NEC、上海德爾福、武漢東風汽車、江蘇東風起亞、江蘇麥格納、安徽康佳電器、、安徽博西華、上海奧托立夫、浙江海信惠爾浦、沈陽寶馬汽車、上海大金空調、遼寧大連固特異輪胎、長春大眾集團、湖北武漢佛吉亞、上汽集團、吉林一汽集團、廣西上汽通用五菱、廣西玉林重工、江西長力股份 北京北汽福田、深圳中興通迅、福建新能源科技、湖南三一重工、蘇州恩斯克軸承、河北天威光伏、武漢哈金森、蘇州力特奧維斯、重慶 嘉陵集團 福建奔馳汽車、遼寧大連大眾變速箱 廣東廣州京信通信、深圳中興通訊 河南利達光電 河南新鄉豫新 河北萊尼、山東萊尼 、山東勝地、陜西中航、湖南時代電氣、天津中核
六西格?瑪管理培訓課程公開課視??頻--點擊圖片即觀看好看視?頻或優酷視?頻相應培訓視頻
六西格?瑪管理培訓課程公開課視??頻--點擊圖片即觀看好看視?頻或優酷視?頻相應培訓視頻
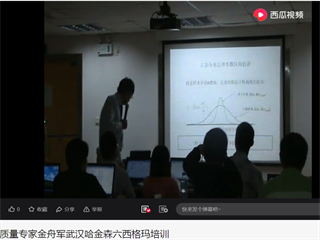

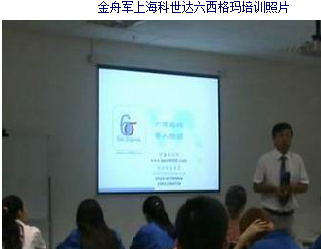
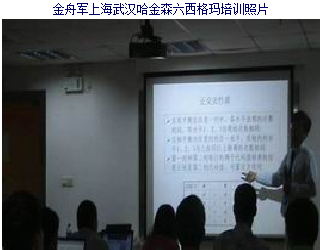
六西格瑪黑帶
培訓課程大綱
培訓課程大綱
1.培訓目的 通過本課程的學習, 使學員能掌握6SIGMA 工具,進行過程的持續改進。
2.培訓對象 產品及工藝開發、質量及現場管理、6SIGMA 項目人員
3.課程內容
1) 六西格瑪概述
什么是六西格瑪管理
六西格瑪發展
DMAIC過程
六西格瑪過程模式
六西格瑪質量水平與不合格率PPM
2)定義Define 階段
項目背景
征狀 問題 原因
確定改進項目
制定問題解決目標原則
一次解決一個問題
項目的收益
項目團隊
組成團隊資格與時間
組成團隊的原則
團隊職責矩陣
6SIGMA 質量的經濟性特征
劣質成本分析(COPQ,cost of poor quality )
有形損失與無形損失 金舟軍原創 抄襲必告
傳統質量改進的成本觀念
經典最佳質量成本模型圖6SIGMA最佳質量成本模型圖
6SIGMA水平與劣質成本關系
6SIGMA成本質量指標
質量成本三級科目
預防成本
鑒定成本 內部故障成本
外部故障成本
外部質量保證成本
3)測量Measure 階段
問題綠Y 的確定
質量特性值
缺陷數
事件次數-特性值
應力極限轉換
能量工具解決技術問題
項目定義樹
產品變差
直方圖描述產品特性分布
基于分布分析原因
直方圖MINITAB操作
分布類型和統計量
總體分布統計量
算術平均數 總體方差 總體標準差
樣本分布統計量
樣本均值 樣本方差 樣本標準差
樣本分布統計量Excel示例
正態分布函數
分布密度函數
正態分布的密度函數
正態分布概率
Excel正態分布概率示例NORMDIST
正態分布總體參數估計
正態分布總體參數點估計
均值的無偏估計
總體方差的無偏估計
標準差的無偏估計
對估計量的評價
用Rbar方法估計
中心極限定理
樣本均值的抽樣變差
抽樣分布--中心極限定理
總體為正態分布
總體為非正態分布
質量損失函數
福特公司案例
美國產品與日本產品比較
“目標柱”思維方式VS損失函數思維方式
油泵柱塞損失函數
田口損失函數思維模型
兩個質量指標-符合性質量和質量損失函數
損失函數與返修率
損失函數敏感程度
損失函數的減少
過程能力指數Cpk和過程性能指數Ppk
過程性能指數的提高
兩種減少過程變差方法
過程控制-現場措施
過程改進-系統措施
現場不可控制的-普通原因變差
現場可控制的-特殊原因變差
過程能力—過程固有變差-普通原因產生過程變差σc
過程固有變差計算的兩個條件
GRR分析
確定重復性和再現性-均值極差法
重復性和再現性-極差法分析實驗方案的設計
GRR過程控制和產品檢驗接受準則
圖形分析法:極差圖、均值圖及其圖形分析
GRR分析minitab及Excel應用
典型的測量系統極差法案例
確定重復性和再現性-均值極差法
重復性和再現性分析minitab
及Excel應用重復性和再現性原因分析
確定重復性和再現性-方差分析法(ANOVA)
重復性和再現性方差分析法實驗方案的設計
零件、評價人、交互作用和量具變差ANOVAminitab
及Excel應用
典型的測量系統方差分析法案例
假設檢驗分析-交叉表方法
交叉表Kappa值計算
評價人之間的差異
評價人與基準的一致性
95%置信區間的算法
分析Analysis 階段
問題解決樹
找球游戲啟示
基于事實結果反向搜索
搜索根本原因三步法
可能原因
最有可能原因
根本原因
Is / Is Not描述問題
變差族分析
多層變差圖在Red X策略的位置
多層變差圖Multi-Vari Chart
多層變差模型
分層法調查表
多層變差圖
變差過程分析案例
集中圖案例
變差族顯示變化是時間性
5).改進Improve 階段
驗證哪些因子為重要因子
防錯兩種功能
預防性維護、預測性維護
驗證糾正措施的方法
標準化作業SOP
B vs. C比較
B vs. C流程
DOE課程內容
1.DOE設計和開發的應用
質量控制四個階段
質量特性的期望值
產品設計和開發
產品三次設計
過程設計和開發
過程三次設計和開發
DOE基礎部分
試驗設計發展三個階段
實驗設計的目的
實驗設計四種方法
因子輪換法
因子輪換法缺點
一次一因子實驗法
什么是實驗設計
實驗設計的術語
因果關系與函數關系
編碼值與真實值
一次一因子實驗法回歸方程
一次一因子實驗法
數理統計基礎
總體分布統計量
正態分布的密度函數
正態分布概率
制造彈簧實例
中心極限定理
單值比較&均值比較
全因子實驗法
無交互作用的正交實驗設計
有交互作用的正交實驗設計
正交表性質
兩水平全因子設計
全因子實驗案例
全因子實驗設計特點
部分因子實驗設計
正交部分因子實驗
實驗設計要解決的問題
部分因子設計兩種生成方法
正交部分因子實驗案例
正交表分辨率
正交表五級分辨率
正交表四級分辨率
正交表三級分辨率
正交表分辨率
交互作用DOE案例1
交互作用DOE案例2
田口式正交表實驗法
正交表分類
無交互作用正交表
三水平正交表
水平不等的實驗設計
正交設計回歸分析
正交設計回歸方程系數的檢驗
回歸模型的檢驗
變量搜索技術VariablesSearch
變量搜索在RedX策略的位置
變量和水平的確定
顯著性檢驗
變量搜索的確定工藝參數
變量搜索的分析流程和案例
第1階段球場 金舟軍原創抄襲必告
第2階段排除
第3階段誘騙實驗
第4階段分析
MINITAB軟件實現正交設計
啟動 MINITAB 項目&工作表
MINITAB軟件DOE菜單
MINITAB軟件創建因子設計
創建因子設計
自定義因子設計
實驗分組(Blocking)
實驗隨機化(Randomization)
默認生成元與指定生成元
部分因子設計分辨率
全因子設計
部分因子設計
因子效應的混淆及直交表實驗的分辨率
部分因子設計分辨率
別名結構
MINITAB軟件多元線性回歸
系數顯著性檢驗
t值檢驗與p值檢驗
討論-t值檢驗與p值檢驗的關系
MINITAB軟件全因子設計
創建因子設計
已編碼與未編碼單位
全因子設計解釋結果
自定義因子設計
討論-將已編碼轉為未編碼單位
MINITAB軟件分析因子設計
解釋分析因子設計結果
效應和系數的估計結果
系數估計,使用未編碼單位的數據
設計點的擬合值
MINITAB軟件篩選實驗Plackett - Burman Design
生成篩選實驗
分析篩選實驗
篩選實驗案例
MINITAB軟件因子設計中添加中心點
MINITAB回歸模型
因子設計中添加中心點
數字和文本因子組合中心點
添加中心點因子設計分析
增加中心點檢驗彎曲
MINITAB軟件等值線/曲面圖
等值線/曲面圖
重疊等值線圖
討論-分析一個重疊等值線圖
MINITAB軟件響應優化
因子設計的重疊等值線圖
因子設計的響應優化
響應優化權重值
響應優化重要性值
選擇最優設計
MINITAB軟件中心組合設計
中心復合設計的特點
中心復合設計的步驟
立方點、軸向點和中心點
創建中心復合設計
中心復合設計分析
DOE實戰案例部分
響應值Y的選取
響應值Y改進目標的確定
實驗設計精度和次數的關系
正交試驗設計的基本步驟
試驗設計計劃制定
試驗水平和次數的確定
篩選試驗設計
優化試驗
確認試驗設計
6).控制Control 階段
項目收益核算
Xbar-R控制圖
控制圖原理- 抽樣變差
控制圖原理- 3S原理
控制圖原理- R抽樣變差
控制圖的兩類錯誤
控制圖基本構造要素
事件記錄
控制圖4W2H
過程改進循環
控制圖兩個階段
計量型控制圖
分析用控制圖
計算平均值和控制限
使用控制圖的準備
Xbar-R圖的案例
制定抽樣計劃
控制圖靈敏度與子組容量
子組容量大小
子組數大小
控制圖統計分析
判異準則
分析極差圖
分析均值圖
識別并標注特殊原因
評價過程能力
過程能力和過程性能計算
過程能力和過程性能計算前提條件
過程處于統計穩定狀態, 即不違反SPC規則;
過程和各測量值服從正態分布;
工程及其它規范準確地代表顧客的需求;
設計目標值位于規范的中心;
測量變差相對較小
能力指數計算實例
過程能力指數研究時機
公差中心與目標不重合時的過程能力指數Cpm
過程受控和過程能力
過程受控
過程能力
減少普通原因持續改進過程潛力
減少特殊原因持續改進過程表現
能力指數計算流程
能力指數計算實例
控制用控制圖監控過程
控制用控制圖控制限
控制中心值
單值和移動極差圖(X—MR)
單值和移動極差圖應用條件
單值和移動極差圖案例
設備能力指數Cmk模型建立及計算
設備能力研究范圍
計算Cmk流程
Minitab計算Cmk
預防維護
設備周期性計劃維修
計劃維護
基于產品要求制定周期維護計劃
日常點檢
潤滑維護
機械設備換油及潤滑保養記錄表
定期檢查
案例討論-怎樣確定周期維護計劃的舟周期
預測性維護
故障概率與MTBF
預測性維護技術手段
預測性維護實施方法和實例
預測性維護實施流程
磨損分析、電路回路分析、溫升分析、熱相分析、振動分析等案例。
過程檢驗控制
產品檢驗的兩個功能
三種檢驗方法
判斷檢驗
信息檢驗
抽樣檢驗與全檢
檢驗過程風險
自檢系統
后續檢查系統
溯源檢驗
案例討論-為什么信息檢驗好過判斷檢驗
溯源檢驗
溯源檢驗原理
溯源檢驗循環
溯源檢驗案例
案例討論-為什么信息檢驗好過判斷檢驗
防錯Poka-yoke
生活中的防錯
過程不符合的根本原因
人員三個方面的錯誤
人無法避免的錯誤
防錯定義
防錯應該是廉價的
零缺陷質量控制系統
過程中防錯VS檢驗中防錯
案例討論-針對一過程釆取一個廉價的防錯措施
防錯兩種功能
控制功能
警告功能
案例討論-為什么控制功能好過警告功能
三種類型防錯方法
觸碰式防錯法
固定數值防錯法
動作步驟探測防錯法
三. 課程學時: 每天6小時 黑帶共10天 , 綠帶5天(不包括doe、spc、msa)
一.培訓對象6SIGMA項目、TS和ISO質量體系的質量及技術人員
二.課程公開課內容
1.六西格瑪簡介
案例討論-.六西格瑪DMAIC能用于產品設計嗎 金舟軍原創抄襲必告
2.六西格瑪定義Define階段(0.5天)
排列圖、趨勢圖、FTA樹圖和甘特圖
流程識別與改進 金舟軍原創抄襲必告
質量目標SMART原則
質量成本、質量金經濟性指南
QFD質量功能展開識別顧客要求
排列圖MINITAB軟件應用
案例討論-排列圖怎么樣用于定義項目
3.六西格瑪測量Measure階段(1.5天)
過程流程圖
因果圖、KCC和KPC矩陣 金舟軍原創抄襲必告
PFMEA
MSA:測量系統線性、偏倚、R&R、穩定性
MSA五性MINITAB軟件應用
SPC、直方圖、正態性檢驗
SPC、直方圖、正態性檢驗MINITAB軟件應用
過程Cpk、Ppk計算
Cpk、Ppk的MINITAB軟件計算
案例討論-計算Ppk為什么要做正態性檢驗
4.六西格瑪分析Analysis階段(2天)金舟軍原創抄襲必告
假設檢驗:Z、T檢驗
Z、T檢驗MINITAB軟件應用
相關性和回歸分析
回歸分析MINITAB軟件舟應用
方差分析(ANOVA) 金舟軍原創抄襲必告
方差分析MINITAB軟件應用
新老七種質量工具
案例討論-方差分析的應用范圍
5.六西格瑪改進Improve階段(2天)
試驗設計(DOE)
系統設計、參數設計、公差設計
質量損失函數
同步工程DFM/A
6Sigma精益生產
5WHY工具
試驗設計(DOE)MINITAB軟件應用
案例討論-怎樣用試驗設計做參數設計金舟軍原創抄襲必告
6.控制Control階段(1天)
控制計劃、標準化作業SOP
SPC、防錯poka-yoke
TPM&設備FMEA
預防性維護、預測性維護
案例討論-控制計劃控制方法包括控制圖嗎
6SIGMA項目案例金講解(1天)
三.課程學時:每天7小時共8天
六西格設計DFSS培訓
課程大綱
一.培訓目的通過本課程的學習,使學員能了解DFSS概況,DFSS的IDOV六西格設計流程和各階段應用的工具。
二.培訓對象產品及工藝開發、質量及現場管理、6SIGMA項目人員
三.課程學時每天七小時2-8天
四.培訓內容
1.6SIGMA概況
六西格瑪管理發展歷史
六西格瑪質量
六西格瑪質量與財務結果
六西格瑪質量水平3.4ppm金舟軍原創抄襲必告
劣質成本COPQ
六西格設計DFSS過程
IDOV流程Identify、Design、Optimize、Verify
2.1.Identify識別流程
市場評估
競爭性評估/基準測試結果
想法的軍優先順序
戰略定位
客戶優先要求
優先CTC’s
第一階段質量屋
初始性能記分卡
2.2.Identify識別工具
驗證客戶需求
項目舟章程
戰略計劃
跨職能團隊
客戶心聲
基準
卡諾模型
問卷
焦點組
采訪 金舟軍原創抄襲必告
網絡搜索
歷史數據分析
實驗設計
質量功能展開
成對比較
層次分析法
性能記分卡
流程圖
fmea
3.1Design設計流程
概念開發
初步設計風險評估
優先考慮產品設計特點
第二階段質量屋
性能/過程記分卡
功能轉換
3.2.Design設計工具
CTC’s指定規格
客戶訪談
制定設計概念
TRIZ
fmea
故障樹分析
頭腦風暴
qfd
功能轉換
實驗設計
確定性模擬器
離散事件模擬
置信區間 金舟軍原創抄襲必告
假設檢驗
MSA
計算機輔助設計
計算機輔助工程
4.1.模塊四:Optimize優化流程
過程開發
可制造性評估
工藝能力研究
可靠性研究
優化設計
X的公差
完整記分卡
虛擬樣機
4.2.模塊四:Optimize優化工具
直方圖
分布分析
經驗數據分布
預期價值分析(EVA)
非正常輸出分布
實驗設計
多響應優化
穩健的設計開發
使用交互繪圖
使用等高線圖
參數設計
公差分配
可制造性和裝配設計
防錯
產品性能預測
部件、過程和軟件記分卡
風險評估
可靠性
5.1.Verify驗證流程
原型
工藝驗證
產品驗證
有能力的產品和工藝
控制計劃
商業化支持
5.2.Verify驗證工具
靈敏度分析
間隙分析
fmea
故障樹金分析
控制計劃
運行/控制圖表
防錯
MSA
反應計劃
朱蘭談六標準差
朱蘭(Joseph M. Juran)生于1904年,今年已近99歲高齡,他一生致力質量志業,著作甚豐,出版書籍包括:朱蘭質量 手冊、質量規劃與分析、創造質量、管理突破…等十種,其中「朱蘭質量手冊」已發行到第5版,早已成為質量專家學者們的必備的案頭書。
他曾于50年代中期赴日傳授質量管理,對日本質量革命有啟迪之功,80年代他促成了美國「馬康巴立治國家質量獎」的設置 ,對美國質量復興運動亦有不可磨滅的貢獻,1986年他創設「朱蘭研究院」與「朱蘭基金會」(即現在明尼蘇達大學的朱蘭中 心),如此可使他的質量志業,永續流傳。由于成就杰出,是國際公認的二十世紀以來最偉大的質量思想家之一。
朱蘭已于1993年從公眾生活中退休,但他仍偶爾演講、寫作,以及忙于撰寫回憶錄。去年六月間,質量文摘的主編史考特 派頓(Scott M. Paton)在紐約朱蘭的家中訪問了他。依據派頓的描述:「盡管當時他已屆98高齡,但身體仍舊硬朗,心智依 然敏銳。雖然有時回答地很小心,但他從未詞不達意。如同我以往與他接觸的幾次訪談中一般,他總是客氣、體貼又幽默。」這
點筆者頗有同感,猶記得1987年參加東京國際品管會議中見到他,當時他已屆83歲,感覺他身裁瘦削略顯佝僂,額頭寬,下巴 窄,鼻梁挺直,眼光溫和有神,我趨前向他表達問候之意,并稱贊他「真了不起」(You’re great!)以表達敬意,他含笑響應 「我每天都在縮小」。(I’m shrinking day by day),一代大師能如此自我調侃,益顯現他平易近人的高貴情操。
朱蘭對六標準差的看法派頓訪談的范圍甚廣,其中引人注目是有關六標準差方面的問題,這個題目,在勞勃?史雷特著 「復制奇異」中有具體的描 述。其中文版于2000年9月在臺灣發行后,帶動了國內探索六標準差的風潮,許多專家學者們紛紛表達了他們對六標準差的了解 與看法,當然你也會想知道大師對它的見解,且看他怎么說。
1. 派頓問朱蘭對六標準差的看法
朱蘭說:「就我所見,這是質量改進的基本說法,并無新意。它包括了我們所謂的輔導員。他們采用了更炫的名詞,像具有 不同顏色的帶(注1)。我認為這概念值得單獨提出,創造一些非常有用的專家。再說一次,那并非新主意。美國質量學會早就 建立了證書制,如可靠度工程師。現在經美國質量學會頒發的證書,已超過10萬人。多數人甚至不了解六個標準差所指為何。它
系指一個目標。一個疵病非常少,少到以百萬為單位的目標。我們習慣以疵病百分數來思考。例如,百分之一的疵病系指每一百 萬單位中有一萬個缺點;對三或四個而言,距離是差得很多(注2)。基本上,此概念相當好,但沒什么新意。它最初由熱切追 求卓越質量的摩托羅拉前總裁Bob Galvin開始,若干年前,他給了他組織改進質量與以階乘(orders of magnitude.)為準的降 低疵病水平的工作,現在,從幾個疵病百分數降到每百萬分之三,這是第四階乘。六標準差之名來自我們所謂的制程能力量測 (注3),量測制程中固有的一致性。在達成六個標準差改進的標記下,常用的固有工具之一是,制程能力的概念。此時,就我
所知,這制程能力可回溯到1926年,當時我是西方電氣的一個年輕工程師。我遇到個問題,而我因為發現每一制程都可依其固有 的一致性予以量化,進而解決了問題。這可以和允收界限相比,看制程是否可承擔工作。此外,你同時可以看到制程是否有能 力,但方向被誤導。如果不是再創者,我是這個觀念的發明者。」
2 派頓再問:「有許多營銷到處大肆宣傳六個標準差,就如ISO9000一樣。您對此有感覺如何?」
朱蘭說:「我贊成用各種方法來改進質量。目前,我認為真正將六標準差發揚光大的是通用電器公司(GE)。他們強烈要求 從事質量改進,我認為Jack Welch是受到Bob Galvin在摩托羅拉所做所為的影響,他采取同樣方式。然后,他將節省數十億美元 與巨大的喜悅與成果公諸于世。這就吸引了許多新聞媒體的青睞,要想忽視它都很難。我不喜歡這種大肆宣傳的做法,而且我也 不認為這種大肆宣傳的做法會長久存在。某些像改進過程成功的事情,一次又一次地得到標志,這些標志來來去去,但基本概念 卻不會變動。總會有些找到新標簽的市場商人,找到蔚為風尚的方法,在新標簽下作我們過去所做的事情,一旦退燒他就走人。」
朱蘭行事低調,不喜歡夸大宣傳的做法,因為他看多了管理市場上許多忽起忽落的所謂的新手法,各有其一定的壽命周期,逾此 期限,就會自然消失無痕。多年前再造工程(Reengineering)盛行時,就有人指出那不過是三十多年前GE公司發動組織改造 (Reconstruction)與朱蘭所提出「突破順序」(Breakthrough sequences)的翻版,若我們再看朱蘭對突破一詞所下「動態 的、積極的行動以獲得更新更高的績效水平」的定義,那與追求6σ質量水平的觀念有何不同?明乎此,你就會同意朱蘭為什么會 說「就我所見,這是質量改進的基本說法,并無新意」的道理。